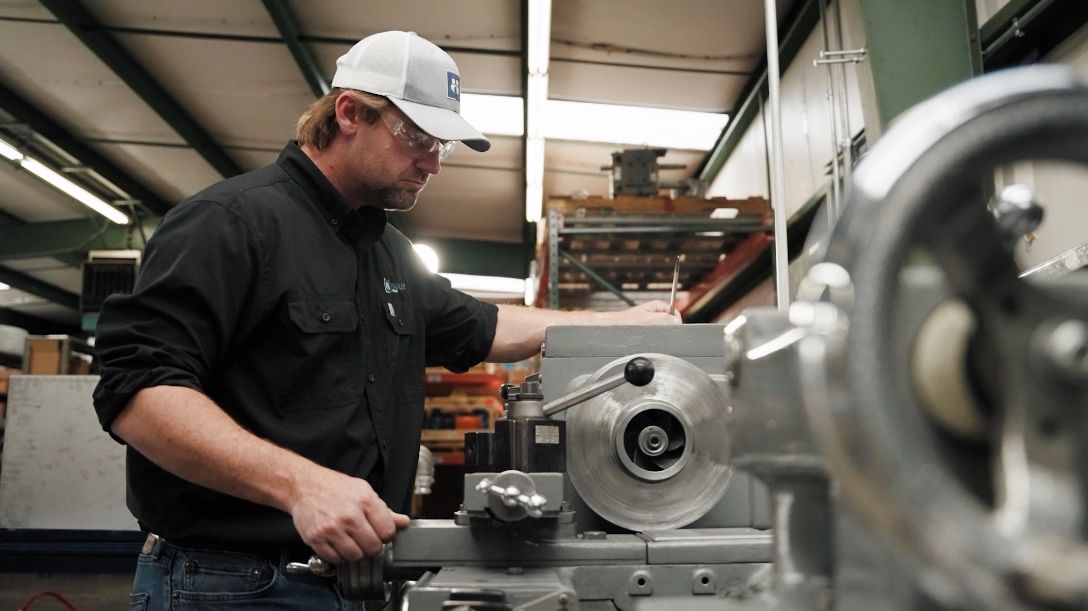
Precision Machining
Having properly sized and balanced impellers makes an impactful difference in the accuracy and efficiency of your pump. Our technicians are trained to trim and balance impellers to ISO standards, alleviating problems in your rotating equipment. Balancing impellers zeros out unbalance and eccentricity, reducing cavitation and bearing wear. Having properly sized impellers helps to save energy, reduce costs, and extend your equipment's lifespan.
Operational Benefits
Trimming
Adjusting the impeller size can optimize the pump's efficiency by reducing the pump head and lowering the flow rate; therefore, allowing the system to become customizable to the needs of the application. When a pump operates close to its best efficiency point (BEP), it consumes less energy, reduces operating costs, and prolongs the lifespan of the pump. Trimming the impeller can influence the Net Positive Suction Head (NPSH) required for the pump to operate without cavitation. Trimming allows for control of the NPSH characteristics to ensure the pump doesn't suffer from cavitation.
Balancing
Tighter balance tolerances significantly reduce vibration levels and prevent premature bearing and ring wear. Balancing your rotating equipment is a must to ensure correct operation of your machine at a high level of efficiency and to extend the longevity of your pump. To reach our high standard of quality control, we balance every impeller that comes through our door. Our Asaki precision balance machine, operating with our EasyBalance computer software, work together to ensure precise measurements and accurate data reports.